Wednesday, 15 August 2012
Types of Underwater Welding
Do you like this story?
International interests to develop and utilize oceans which cover 70% of the earth and its resources such as development of offshore gas and oil field, fisheries multiplication, large offshore construction and mineral resources, mining in the sea bottom,etc; have let to the development of underwater welding. Underwater welding has been used for temporary repair work caused by ships collisions, unexpected accidents, corrosion and other maintenance works.
Types of Underwater Welding:
Following are the types of underwater welding:
1. Wet welding
2. Dry welding :
1. Hyperbaric welding
2. Cavity welding
1.Wet welding:
Wet welding is carried out directly in water using waterproof stick electrodes. Arc welds made underwater, without any precautions to protect the arc from the surrounding water, suffer because of hardness and brittleness resulting from the quenching effect of water. Further, hydrogen evolved due to dissociation of water in the arc, dissolves in the weld metal with a consequent tendency towards cracking.
2. Dry welding:
Dry welding needs a pressurized enclosure having controlled atmosphere. Weld metal is not in direct contact with water. Dry welding produces very good welds, but the process is expensive.
Advantages of dry weld arc:
- Reduced hydrogen problem of the environment.
- Improvement in stability of welding operation.
- Lower weld metal and base metal quench rates.
- Weld strength and ductility comparable to surface welds.
Types of Dry welding:
- Hyperbaric welding: Welding is carried out in a dry chamber constructed around the joint to be welded. Water is expelled by providing a gaseous atmosphere in the chamber at pressure equal to water pressure and so keeping the water out. This process is termed as habitate welding when used for joining large pipelines where the chamber is large, filled with a breathable atmosphere and equipped with a life support system for the operator.
- The necessity for seals between the chamber and the structure to be welded is a practical difficulty.
- Increase in pressure as depth increases introduces problems both for the welding process and for divers.
- Cavity welding: Cavity welding is another approach to weld in a water free environment. In this process the conventional arrangements for feeding wire and shielding gas are surrounded by a means for introducing a cavity gas and the whole is surrounded by a trumpet shaped nozzle through which a high velocity water jet passes. Cavity method avoids the need for a habitate chamber and it lends itself to automatic and remote control. This process is very suitable for flat structure where butt-welds with a backup strip can be welded in the flat or overhead positions. Cavity welding does not appear to be suitable for unbacked pipelines butt joints nor for lap joints which have accounted for the majority of underwater welding work.
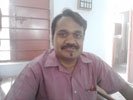
This post was written by: Sanjay Verma
Sanjay Verma is an experienced mechanical engineer and a lecturer. In this blog he shares his knowledge about various subjects of mechanical engineering. Follow him on Google+