Saturday, 1 September 2012
General Layout Of A Diesel Engine Power Plant
Do you like this story?
Figure shows the general layout of a diesel engine power plant. The engine and its various auxiliaries systems are depicted with their proper positions. The flow path of air, fuel and gas are shown by arrows. The plant consists of the following:
- Engine
- Air Intake system
- Exhaust system
- Fuel system
- Fuel Injection system
- Cooling system
- Lubrication system
- Starting system
Principal parts of a diesel engine:
Figure shows a cross-section of an air cooled IC engine depicting the principal parts. Generally, for stand-by plant, water cooled engine is preferred but where there is scarcity of water or in mobile power plants, air cooled engine is preferred. The principal parts are cylinder, cylinder head, piston, inlet valve, Inlet port, Exhaust valve, Valve spring, cooling fins, wrist pin, connecting rod, crankcase, crankpin, crank, crankshaft.
Air Intake System:
The function of air intake system is to convey fresh air through louvres and air filter to the cylinder via intake manifold. In order to augment the power, supercharger is fitted in between the filter and engine and the super charger is driven by the engine itself.
Exhaust system:
The purpose of exhaust system is to discharge the engine exhaust to the atmosphere with minimum noise. Figure shows the exhaust system. The exhaust manifold connects the engine cylinder exhaust outlet to the exhaust pipe which is provided with a muffler or silencer to dampen the fluctuating pressure of the exhaust line which in turn reduces most of the noise which may result if gases are discharged directly to the atmosphere. It is advisable to use flexible tubing system for exhaust pipe to take up the facts of expansion due to high temperature and to isolate the exhaust system from the engine vibration.
Appreciable amount of heat from the engine exhaust goes as a waste. In order to utilize this, a heat recovery steam generator (HRSG) may be used to generate low pressure steam for process work.
Fuel handing system:
Figure shows the fuel handling system of a diesel engine power plant. The fuel oil may be delivered at the plant site by many means such as trucks, railway wagons or barges and oil tankers. With the help of unloading facility, the fuel oil is delivered to the main tanks from where oil is pumped to small service storage tank known as engine day tank through strainers. This day tank has the capacity to store oil equivalent to about 8 hours consumption. In order to reduce the pumping power input, oil is heated either by hot water or steam which reduces viscosity and so the power input.
Fuel Injection system:
It is supposed to be the heart of diesel engine and its failure means stopping of the engine. The fuel injection system performs the following functions:
- It filter the fuel insuring oil free from dirt.
- It meters the correct quantity of fuel to be injected in each cylinder.
- It times the injection process in relation to the crankshaft revolution.
- It regulates the fuel supply.
- It atomizes finely the fuel oil for better mixing with the hot air leading to efficient combustion.
- It distributes, the atomized fuel properly in the combustion chamber.
- Common rail injection system
- Individual pump injection system.
- Distributed system.
2. Individual pump injection system: As the name implies, the system has an independent high pressure pump for each cylinder which meters, pumps and controls the timing of fuel injection as shown in figure. Each cylinder is provided with one injector and the pump and injector may be integrated as one unit. The fuel is brought to the individual pump from storage tank through course filter, low pressure pump and fine filter. The high pressure pump is equipped with a control mechanism and at the proper time, a rocker arm actuates the plunger and thus injects the fuel into the cylinder. The amount of fuel injected is regulated by the effective stroke of the plunger. It is the most popular fuel injection system in practice.
3. Distributed system: Figure shows arrangement of distributed system. In this system a metering and high pressure pump is used to pump the metered quantity of fuel on the rotating distributor which distributes the fuel to the individual cylinder at the correct timing. The number of injection stroke per cycle for the pump is equal to the number of cylinders. The fuel is fed to the high pressure pump from storage tank through course filter, IP pump and fine filter. Since the metering and timing of injection is accomplished by one plunger, equal amount of fuel is supplied to each cylinder at the same point in the cycle.
Fuel Injector:
The liquid fuel in the injection system filters into the combustion chamber through the injector. Fuel injector employed in CI engine is of automatic type. It is mounted on the cylinder body at such a location which yields better performance. Quick and complete combustion is insured by a well designed fuel injector. The fuel injector assembly consists of the following:
- Needle or nozzle valve
- A compression ring
- A nozzle
- Injector body
Types of nozzles:
The design of nozzle is mainly based on the types of combustion chamber used insuring proper and efficient combustion of fuel. The type of nozzles used in diesel engines are:
- Single hole
- Multi hole
- Pintle type
- Pintaux type
Cooling system:
During combustion process, the pick gas temperature in the cylinder of an IC engine is of the order of 2500K. Maximum metal temperature for the inside of the combustion chamber space are limited to much lower values than the gas temperature by a large number of considerations and thus cooling for the cylinder head, cylinder and piston must therefore be provided.
![]() |
Force circulation cooling system |
- Open cooling system: This system is applicable only where plenty of water is available. The water from the storage tank is directly supplied through an inlet valve to the engine cooling water jacket. The hot water coming out of the engine is not cooled for reuse but it is discharged.
- Natural circulation system: The system is closed one and designed so that the water may circulate naturally because of the difference in density of water at different temperatures.It consists of water jacket, radiator and fan. When the water is heated, its density decreases and it tends to rise, while the colder molecules tend to sink. Circulation of water then is obtained as the water heated in the water jacket tends to rise and the water cooled in the radiator with the help of air over the radiator either by ram effect or by fan or jointly tends to sink. The direction of natural circulation which is slow is shown by arrows.
- Force circulation cooling system: Figure shows force circulation cooling system which is closed one. The system consists of pump, water jacket in the cylinder, radiator, fan and a thermostat. The coolant is circulated through the cylinder jacket with the help of a pump which is usually a centrifugal type, and driven by the engine. A function of thermostat which is fitted in the upper hose connection initially prevents the circulation of water below a certain temperature, usually upto 85C through the radiation so that water gets heated up quickly. Stand-by diesel power plant upto 200 kVA use this type of cooling.
Lubrication system:
The purpose of lubrication system is to provide sufficient quantity of cool filtered oil to give positive and adequate lubrication to all the moving parts of the engine. The lubrication system is classified as:
1. Mixed lubrication system
2. Wet sump lubrication system:
2. Wet sump lubrication system:
- Splash system
- Pressure feed system
- Splash and pressure feed system
1. Mixed lubrication system: In mixed lubrication system, a small quantity of lubricating oil is mixed in the fuel tank. It is used in two stroke engine.
2. Splash system: The application of this system is limited to only light duty engines as the name implies a splasher or dipper is provided under each connecting rod cap which dips into the oil in the trough at every revolution of crankshaft and oil is splashed all over the anterior of the crankcase.
3. Pressure feed system: The main elements of the system consists of oil in crankcase, strainer, pump, pressure regulator, filter, breather and oil galleries. The oil is drawn from the sump through strainer which prevents foreign particles and is pumped with the help of gear pump submerged in the oil and driven by crankshaft to all the main bearings of the crankshaft through distributing channel. An oil hole is drilled in the crankshaft from the center of each crankpin to the center of an adjacent main journal through which oil can pass from the main bearings to the crankpin bearing. The piston pin receives oil through a hole drilled in the connecting rod. The cylinder walls, tapped roller, cam, piston and piston rings are lubricated by oil spray from around piston pins and the main end connecting rod bearings. A pressure regulator fitted near the delivery point of the pump which opens when the pressure in the system attains a predetermined value in the case of filter clogging of an oil cooled and excess oil is returned back to the sump.
4. Splash and pressure feed system: Figure shows a splash and pressure feed system. In this case, lubricating oil is supplied under pressure to main and camshaft bearing. Splash is also used to lubricate crankpin bearings.

5. Dry sump lubrication system: Figure shows Dry sump lubrication system. In the Dry sump, the supply of oil is carried in an external tank with the help of scavenging pump through strainer and filter, The scavenging pump is placed out of the sump. The capacity of the scavenging pump is always greater than oil feed pump. The supplied tank is usually placed behind the radiator. The dry sump is generally used in large stationary marine engine.
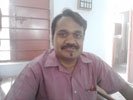
This post was written by: Sanjay Verma
Sanjay Verma is an experienced mechanical engineer and a lecturer. In this blog he shares his knowledge about various subjects of mechanical engineering. Follow him on Google+