Sunday, 19 August 2012
LP stage blading
Do you like this story?
The blades of low pressure stage must be long to cater for the greatly increasing specific volume of steam at the lower pressures. Irrespective of the design of previous stages, the final stage of LP turbine employ little or no reaction at the root and up to about 65% reaction at the tip, this design allows the steam velocity to match the peripheral blade velocity of all radii. in order to dampen vibration long blades may be lased together in batches. It is to be noted that the lasing holes are source of weakness and disturbs the flow path, so it should be avoided as far as possible by better designing against vibration. Sometimes an arched cover bend may be used to brace the blades instead of lacing wires.
LP stage bladings face an another problem of erosion of leading edges due to condensation droplets. In order to avoid this, satellite protection strips which is extremely hard alloys of cobalt, chromium, tungsten and carbon are sometimes braced to the leading edges due to centrifugal action much moisture can be extracted after leaving the moving blades, and provision is made in the cylinder to lead this water away.
Sometimes multi exhaust is used to reduce the length of LP stage bladings invariably, double flow LP turbines are used. A long blade is not suitable because of the following reasons:
Sometimes multi exhaust is used to reduce the length of LP stage bladings invariably, double flow LP turbines are used. A long blade is not suitable because of the following reasons:
- The blade speed varies from root to tip thus there is different blade angles, and if the steam is to flow on the blade without shock, the blade must be twisted. Generally the discharge is axial, they are mainly impulse form at the roots and reaction form at the tips. The inlet angles of blades are varied to allow for change in blade speed.
- The space between the adjacent blades may increase so much from the root to the tip as could affect adversely the steam flow through the blades.
- At the tip speed of 330m/s the stress at the root of blade is great. For this reason and from the point of view of stability, low pressure blades are not made longer than 1/3rd the drum diameter and even then, the blade section is frequently tapered from the tip to the root.
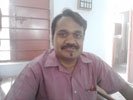
This post was written by: Sanjay Verma
Sanjay Verma is an experienced mechanical engineer and a lecturer. In this blog he shares his knowledge about various subjects of mechanical engineering. Follow him on Google+