Sunday, 9 September 2012
Site Welding : Problems And Solutions -Part2
Do you like this story?
Tools, Equipment and facilities
A compromise between equipment and
production costs must be reached. Specialism welding equipment often
requires experienced operators, who are not likely to be found or cannot
be retained on the permanent basis, owing to non-continuous operations.
Often even though a field training program for the use of such
equipment is provided, the site welders resent change and do not readily
accept new ways of doing things. The delay in overcoming this attitude,
and in acquiring sufficient experience for proficient use of the new
equipment, mean that its potential economic advantages are not realized.
A possible solution to this problem is that operators of such
specialized equipments are hired on a permanent basis and are available
either directly to run the machines or to supervise their operator. Once
a decision has been reached regarding the type and quantity of tools,
equipments and facilities required at a given site, the details of the
field welding shop and arrangement of the equipment can be based on
sound industrial engineering practices.
Environmental effects on site welding
The basis difference between site
welding and manufacturing shop welding is the uncontrolled environment
at the site. At the site, often only crude, temporary shelters can be
justified, usually taking the form of tarpaulins attached to a simple
wooden framework to provide a minimum of shelter. Unless welders are
provided with a safe and reasonably comfortable working platforms or
scaffold, the quality and quantity of work will suffer. Conventional
welders uniforms are unsuited to extremes of climate. The helmet,
leather jackets, and aprons, are unsuited for the dissipation of body
heat in tropical climate. The necessary freedom of movement is impeded
by the usual heavy clothing provided for arctic climates. Possible
improvement is the use of light weight fireproof fabrics for tropical
climates, and electrically heated suits, as used in aircraft practice,
for arctic conditions. The need for the acclimatization of welders is
another factor emphasizing the advantages of employing and training
local labour for site welding. Extremes in environment have their effect
on the weld deposit as well as on the operator. In tropical conditions
the problem of maintenance of preheat may be nicely solved whereas in
arctic climates, it will be accentuated. In frigid locations, the need
for preheat can be minimized by selection of base material and
electrodes with low transition temperatures to reduce the hazards of
brittle fractures. High wind velocities, if there at site, will
considerably effect the welding arcs and hence the weld deposits.
Site welding quality control
A discussion is necessary between the
contractor and the client before work is started, to agree upon the
interpretation of the applicable code or specification as to weld
quality and the manner and extend to which the various inspection tools
are to be employed. The need for this mutual understanding is specially
evident in regard to pipe welding quality, where it is fairly common
practice to apply pressure vessel code criteria of acceptability to pipe
which can only be welded from the outside. Here difficulties frequently
arises out of the welding operators inability to cope with the
irregularities to be expected in mill end pipe. Difference in internal
diameter, out of roundness and inability to rework the route of the
weld, frequently lead to indications on radiographs that tax the ability
of an extremely skilled interpreter to render a satisfactory estimate
of weld quality. Once the welding quality or qualities have been agreed
upon, the problem of producing the welds to these requirements becomes
paramount. The first, vitally important, prerequisite is the accuracy of
fit-up of the parts to be welded. A welder of just adequate skill can
generally make an acceptable weld if he starts with good fit-up, whereas
the most skilled welder will frequently find himself unable to cope
with the situation if the fit-up is poor. The welding supervisor and
inspectors can most profitably pay their way by insuring that the
welders start with well set-up jobs. The depositing of the root weld
pass is a critical factor, whether it be pipe or plate that is being
welded. Where skilled welders are in short supply, they may deposit only
the root passes whereas the remainder of the weld can generally be
completed without difficulty by welders of lesser ability. The maximum
emphases on fit up and root welding applies to all qualities of welding,
but varies in degree with the economics of the quality aimed at. For
example on the lowest quality of welding, accessed only by visual
examination, accurate fit up by experienced pipe fitter and extensive
supervision, inspection, etc cannot be provided at the cost allowed for
this quality of welding. Usually non-destructive tools like radiography,
ultrasonics, magnetic particle inspection, penetrant and fluorescent
dyes, and visual aids can be employed to the extend required to provide
assurance that a given weld quality is being furnished.
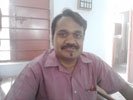
This post was written by: Sanjay Verma
Sanjay Verma is an experienced mechanical engineer and a lecturer. In this blog he shares his knowledge about various subjects of mechanical engineering. Follow him on Google+