Wednesday, 15 August 2012
Gas Welding Processes And Equipments - Oxy-Acetylene Welding
Do you like this story?
Introduction to Gas Welding:
Gas welding is a fusion welding process. It joins metals using the heat of combustion of oxygen/air and fuel gas that is acetylene, hydrogen or butane. The intense heat or flame thus produced melts and fuses together the edges of the parts to be welded with the addition of a filler metal.
Oxy-acetylene welding:
When acetylene is mixed with oxygen in correct proportions in the welding torch and ignited, the flame resulting at the tip of the torch is sufficiently hot to melt and join the parent metal. The oxy-acetylene flame reaches a temperature of about 3200 C and thus can melt all commercial metals which, during welding, actually flow together to form a complete bond. A filler metal rod is generally added to the molten metal pool to build up the seam slightly for greater strength. The maximum temperature of the oxy-acetylene flame is 3100 to 3200 C and the center of the heat concentration is just off the extreme tip of the white cone. Combustion of gas mixture is recognized as taking place in two main stages:
- Stage 1: Oxygen and acetylene in equal proportions by volume burn in the inner white cone. The oxygen combines with carbon of the acetylene and forms carbon monoxide and hydrogen is liberated.
- Stage 2: Upon passing into the outer envelope of the flame two more reactions take place as combustion is completed. The carbon monoxide uses the oxygen supplied from the air surrounding the flame and as a result of burning forms carbon dioxide. The hydrogen also burns with oxygen from atmosphere and forms water vapour. It can be seen that about 2/5 of oxygen necessary for the complete combustion of acetylene is got from the cylinder whereas the rest comes from the surrounding air atmosphere because of the need for supplemental oxygen from the atmosphere, the acetylene oxygen flame cannot be used inside of pipes or structures subjected to oxygen depletion from gas welding. By varying the relative amounts of acetylene and oxygen in the gas mixture in the torch, a welder can produce different flame atmospheres and temperatures as he requires.
Flame adjustment:
- To start with, when the oxy-acetylene gas welding torch is ignited, it gives an acetylene flame in which enough oxygen is drawn in from the atmosphere to burn acetylene partially. From acetylene flame, abundance of free carbon is released into the air. An acetylene flame may be used to apply carbon to mold faces in the foundry, because the carbon acts as an insulator between the molten metal and the mold face.
- As the oxygen valve in the torch is progressively opened, the flame becomes generally luminous. Then the luminous portion contracts towards the welding tip, forming a distinct bright zone within a blue outer envelope. This is a carborising flame and has large excess of acetylene.
- With further increase of oxygen content, the bright zone of the flame contracts farther and is seen to consist of two parts: a brighter inner cone and a pale green feather trailing off its end into the blue envelope, this is reducing flame.
- If at this stage oxygen flow is increased gradually, a certain point will reach where one will notice a distinct change in the sound of the flame and a well-defined white cone will appear near the tip, surrounded by a bluish envelope that is faintly luminous. This is neutral flame. There is an approximate one-to-one mixture of acetylene and oxygen to result a neutral flame.
- Further increase of oxygen content into the mixture will give rise to an oxidising flame.
To extinguish the flame and stop welding:
- When the welding or cutting operation is finished, close the torch acetylene valve first and then turn off the torch oxygen valve.
- Close the oxygen cylinder valve
- Release the pressure in the hose and regulator by opening the oxygen control valve on the torch.
- Release the pressure in the oxygen regulator diaphragm by turning the regulator to the minimum pressure position.
- Close the oxygen control valve on the torch.
- Repeat the same procedure for purging acetylene.
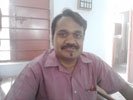
This post was written by: Sanjay Verma
Sanjay Verma is an experienced mechanical engineer and a lecturer. In this blog he shares his knowledge about various subjects of mechanical engineering. Follow him on Google+